Deadly Wastes Canvas
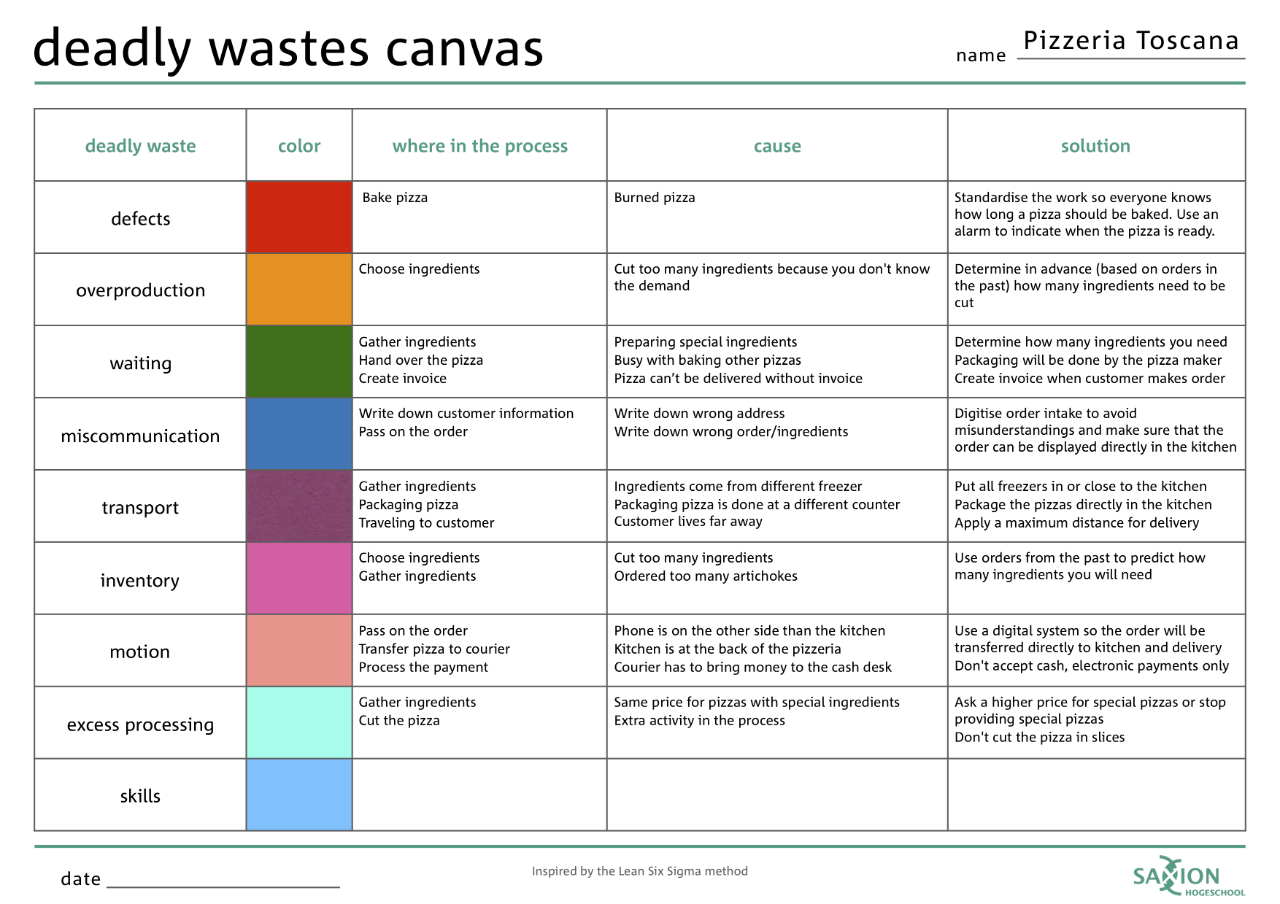
Tips for use
The Deadly Wastes Canvas is most effective if done by a group of people; since discussions will be more fruitful.
Use the Deadly Wastes Canvas to brainstorm how to improve the efficiency of your process. Have a look at the example of Pizzeria Toscana to get inspired and learn from the practical application of this tool.
How to use
Waste can be described as ‘something that adds no value’. With the Deadly Wastes Canvas, you identify the wastes in your process, the causes of these wastes and how to eliminate wastes. Identifying and removing waste helps you to focus on what is valuable to the customer. By following the five steps, you will be able to complete the Deadly Wastes Canvas.
Step 1: select the process
First select a process that you would like to make more efficient. A process is a set of connected activities to achieve a specific result. A process should have a clear start and ending. Examples of processes are hiring personnel, ordering a pizza or drilling a hole.
Step 2: describe the selected process
Describe the selected process as a list of connected activities. Write each activity on a sticky note and place all activities in the right order. When hiring personnel for example, writing the vacancy happens before the job interviews. Connect activities with arrows to indicate the process flow. For more explanation on mapping your process see the Process Journey tool.
Step 3: identify the wastes in your process
From the theory of lean manufacturing we take nine forms of waste that can be represented by the acronym DOWNTIMES:
- Defects: Mistakes that require additional time, resources, and money to fix;
- Overproduction: Production that is more than needed or before it is needed;
- Waiting: Wasted time whenever work in the process has to stop for some reason;
- Non- or miscommunication: Misunderstanding and miscommunication caused by inaccurate or missing information;
- Transportation: Unnecessary movements of products and materials;
- Inventory: Excess products and materials not being processed;
- Motion: Unnecessary movements by people (e.g. walking) or machines;
- Excess processing: More work or higher quality than is required;
- Skills: Not or under-utilizing peoples’ talents, skills and knowledge.
Look again at all activities in your process. For each activity, check if you can find one of the nines types of waste and write the activities down that have waste in the column ‘where in the process’ in the Deadly Wastes Canvas.
Step 4: identify the causes of waste
To be able to solve a problem, it is important to understand where it comes from. When you have found one or more wastes in the activities in your process, think about what causes these wastes and write this down in the column ‘causes’ in the template.
Step 5: come up with solutions
Finally, look for ways to remove waste and improve your process by searching for solutions. You can systematically go through all the identified wastes and look for solutions to improve efficiency.